Info Session Recording
Software and Materials
Overview
There have been lots of awesome works around the topic of bimanual teleoperation and learning from demonstration, employing various human sensing systems and robot embodiments. To name a few, ALOHA, Mobile ALOHA, DexCap, Open-TeleVision, HATO, GELLO, AirExo, UMI, etc.
Currently, research in teleoperation is often conducted using self-designed tasks and evaluations performed by the researchers themselves. While valuable, this approach often overlooks crucial industry metrics such as operational speed, system reliability, cost-effectiveness, and the learning curve for policy implementation.
To address this gap, we provide a set of standardized benchmarking tasks that reflect real-world challenges across multiple dimensions and difficulty levels. The WBCD Competition aims to bridge the gap between academic research and industrial applications by fostering collaboration between researchers and industry professionals to develop practical solutions for real-world challenges.
In this competition, participants can use various methodsโincluding puppeteering, VR, exoskeletons, hand-held grippers, movement-tracking gloves, or algorithmic human hand sensingโto perform challenging and valuable manipulation tasks while collecting data. We will evaluate teams based on their task completion quality, data collection speed, and the performance of policies learned from the collected data.
๐1st WBCD Winners @ICRA2025
Track 1 - ๐ฆLogistic Packing
First Prize
Intelligent Control Lab
Second Prize
TCS Research
Third Prize
MARS Lab, Purdue University
Best Gripper Design Award
ETH ORCA Hand Team
Finalist
Team Spawn
Track 2 - ๐งชBioscience Experiment
Co-First Prize
Create Lab EPFL
Co-First Prize
DexEmbodied
Third Prize
Northwestern Team
Best Application Award
Io-AI
Finalist
Mechanical System Control Lab, UCB
Track 3 - ๐ฝ๏ธTable Services
First Prize
MilkDragon
Second Prize
Egomimic RL2lab Georgia Tech
Third Prize
Starquest
Finalist
EWHAGlab
Best Application Award
FrodoBot AI
Competition Format and Schedule
Competition Phases
Before Conference
- Teams who will join the real competition could ahead of time get in touch with the corresponding hardware sponsor and get familiar with tele-operating real robots
At Conference
- Teams accomplish tasks and collect data using their "budgets" and organizers will assist them to train models using their data, and deploy their model.
Competition Agenda & Room Access Time
Key Dates
Competition tasks
What sets this competition apart is its focus on bimanual manipulation - participants must use teleoperation systems to complete complex tasks requiring coordinated control of two robotic arms. This distinctive approach addresses real-world challenges that demand sophisticated dual-arm manipulation capabilities.
The competition tasks have been carefully crafted by industry sponsors who are leaders in robotics and automation. These challenges represent actual technical hurdles faced in operations with billion-dollar market potential. Each task addresses specific industry needs while pushing the boundaries of current robotic capabilities.
We have incorporated cutting-edge research challenges in the tasks, including:- Manipulation of articulated objects (e.g., paper boxes)
- Handling of delicate materials (e.g., test tubes)
- Control of soft, deformable objects (e.g., linens)
- Interaction with dynamic elements (e.g., conveyor systems)
For the latest competition details, please check out our detailed slides:
Task 1: Packing Challenge in Logistics
Overview
This challenge simulates a real-world automated packing scenario where the robot needs to efficiently transfer items from a moving conveyor system to designated packing containers. The task involves picking items from 10 moving bins on a conveyor belt and organizing them in a target packing bin.
Picking Environment
- 10 picking bins move along conveyor at controlled speed
- Each bin contains identical items
- Items vary between bins (shape, size, weight)
- Time limit of X seconds per bin at picking point
Packing Options
Standard Version
Uses rigid plastic container as packing bin
Advanced Version
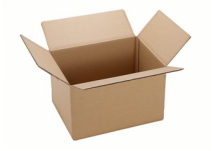
Uses cardboard box with additional box closure requirement
Time Efficiency
- Total picking time (cumulative for 10 items)
- Total packing time (cumulative for 10 placements)
Quality Standards
- The goods in the packing bin should be stacked tightly and neatly, and should not exceed the bin's height
- For the advanced version task, the cardboard box must be properly sealed after packing
Sample Test Scene
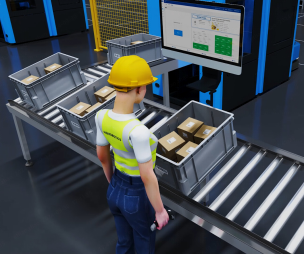
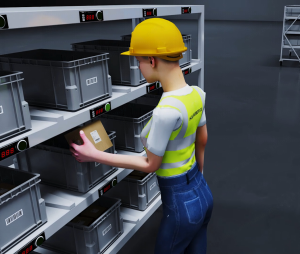
Task 2: Life Science R&D - Experiment Challenge
This challenge focuses on precise laboratory operations, including column chromatography setup and sample handling. The robot must demonstrate careful manipulation of delicate laboratory equipment through three critical stages.
Stage 1: Silica Gel Column Installation
The robot must install a silica gel column using a Luer lock connection system with precision and care.
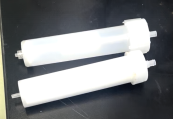
Locate and identify correct silica gel column using vision system
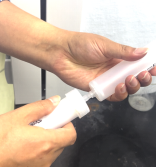
Align and tighten Luer lock connection with precise control
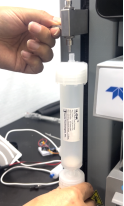
Mount column securely on fixed rack ensuring leak-free connection
Stage 2: Sample Tube Organization
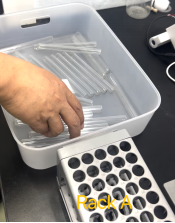
- Transfer tubes from random arrangement to organized grid
- Fill all 30 positions precisely and systematically
- Systematically arrange glass tubes in 5x6 grid on Rack A
Stage 3: Selective Sample Processing
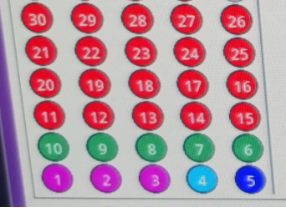
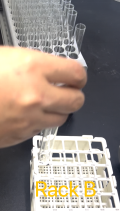
Select and transfer specified tubes based on diagram
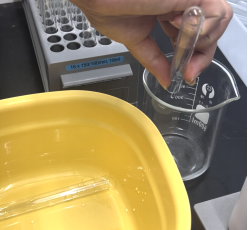
Precisely pour remaining samples into waste container
Technical Precision
- Column alignment and tightening accuracy
- Tube arrangement precision
- Sample selection accuracy
- Liquid handling control
Operational Efficiency
- Task completion speed
- Success rate per subtask
- Error-free execution
- System reliability
Task 3: Table Service Operations
Demonstration of good table service operations and organization skills
Tablecloth Management
Precise unfolding and placement of tablecloth, or systematic folding and storage
Table Clearing
Efficient removal of items and disposal in designated waste containers
Place Settings
Organized placement or collection of plates between table and storage
Evaluation & Scoring System
Virtual Budget Allocation
Each team receives a fixed budget in virtual dollars. Their data collection costs vary based on their teleoperation method, assuming the robots are provided at no cost.
In-Person Control
Side-by-side operation, full information access
High RateClose-Distance Control
Onboard sensors only, minimal latency
Medium RateRemote Control
Onboard sensors, high latency, connection issues
Low RateBonus & Penalty System
Success Bonus
Successful completion: Bonus
Failure Penalty
Catastrophic failure: Penalty applies
Evaluation Criteria
Teleoperation Performance
Quality and speed vs. human baseline
Learning Capability
Data collection efficiency and model performance
Awards ($200,000 Total Pool)
First Place
A robot used in competition or a customized robot solution by hardware sponsor (MSRP $50,000-$60,000)
Second Place
$10,000
Third Place
$5,000
Hardware and Human Resources
The teams are responsible for transporting their teleop sensing system to Atlanta, they can transport their robot, too, if they want to leverage advanced features like force sensing, but since transporting robots is expensive, we have three hardware sponsors, AgileX, ARX, and Galaxea who will provide and transport their robot hardware for the competition.
For those teams who would like to use exoskeleton, hand-held grippers, movement-tracking gloves, or algorithmic human hand sensing for data collection, they are responsible for projecting their data to the action space of the sponsor robot, or their own robot if they transport their robot to Atlanta.
Depending on the funding to be raised, we may hire human operators to help collect data and judge the task completion qualities.
ARX
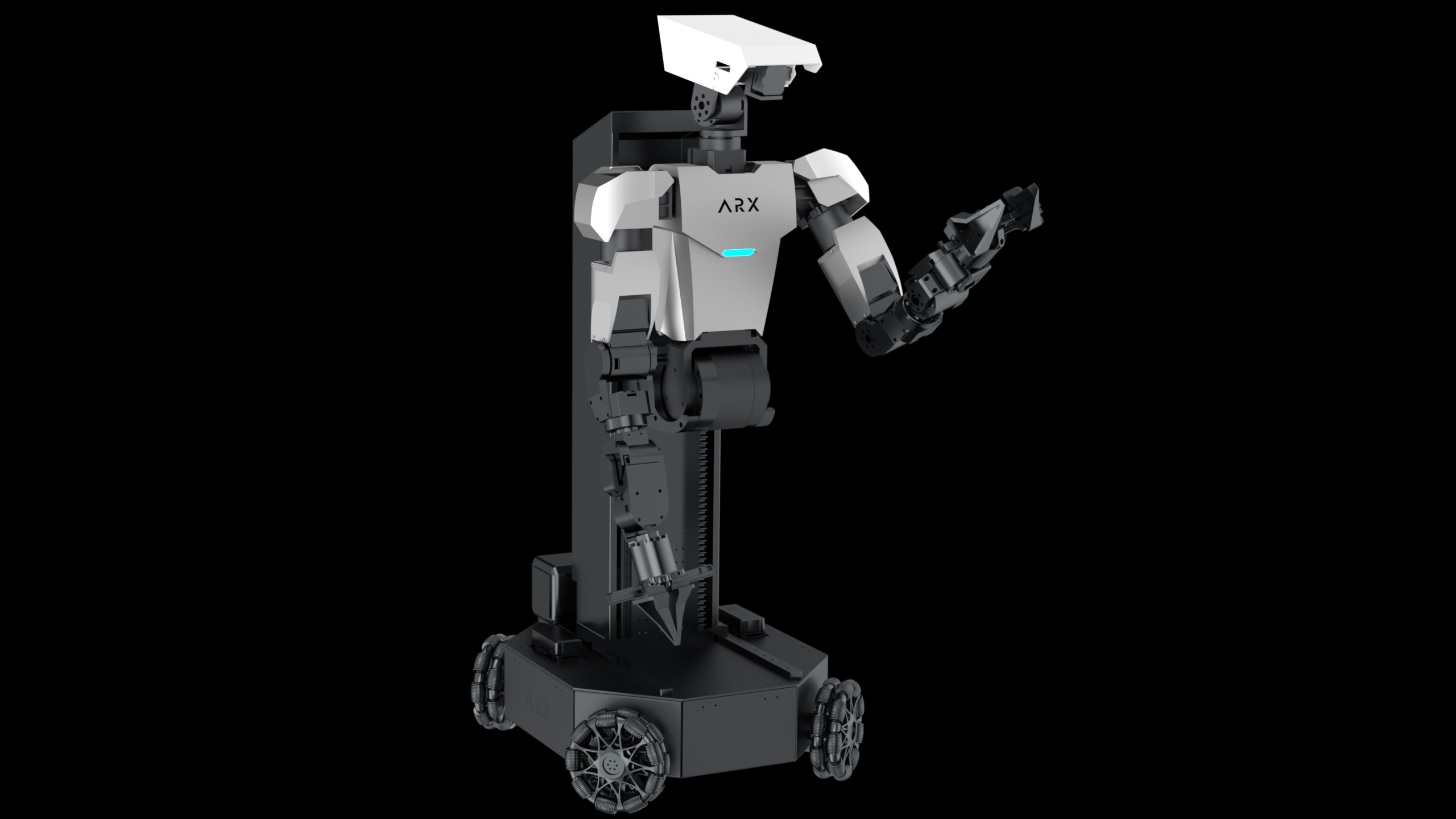
AgileX (ALOHA style bimanual robot system)
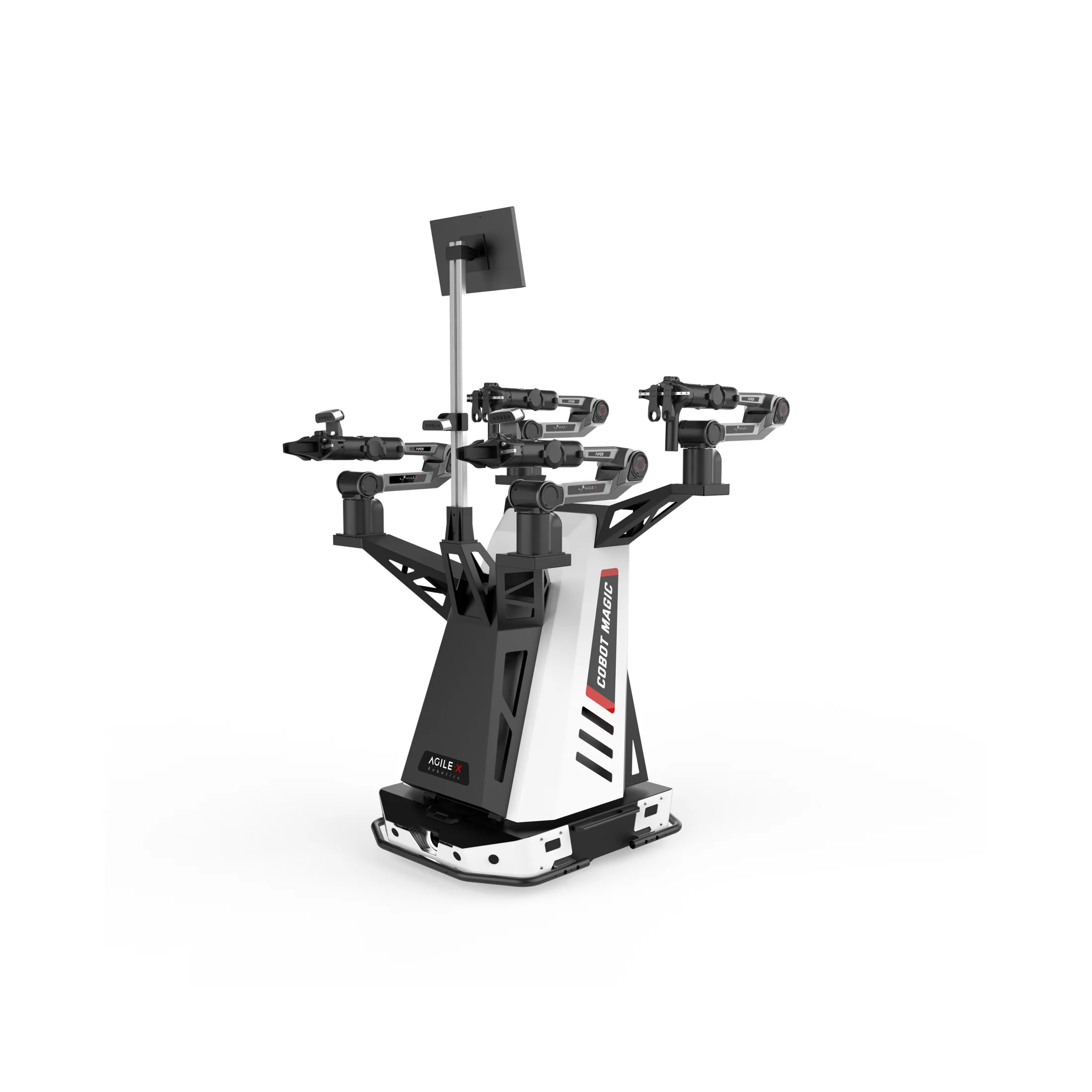
Galaxea (R1)
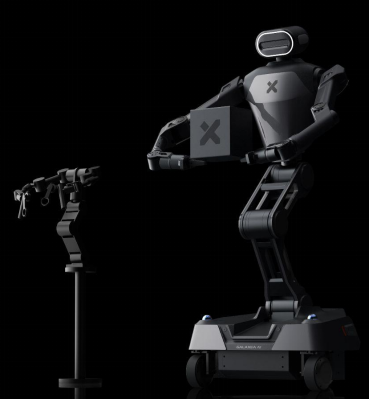
Organizers
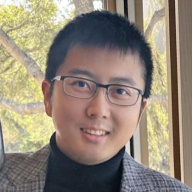
Zhuo Xu
Research Scientist, Google Deepmind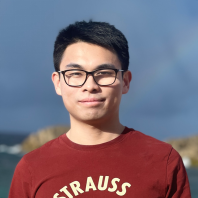
Tao Chen
CEO, Dexmate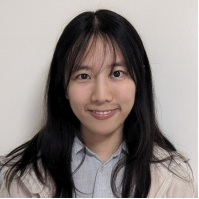
Toru Lin
PhD Candidate, UC Berkeley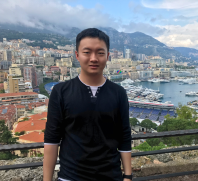
Lingfeng Sun
Research Scientist, Boston Dynamics AI Institute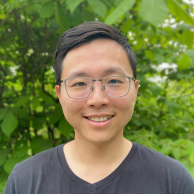
Danfei Xu
Assistant Professor, Georgia Tech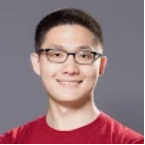
Peter Yu
CTO, XYZ Robotics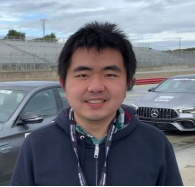
Wenhao Yu
Research Scientist, Google Deepmind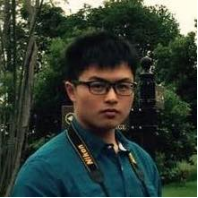
Xinghao Zhu
Research Scientist, Boston Dynamics AI Institute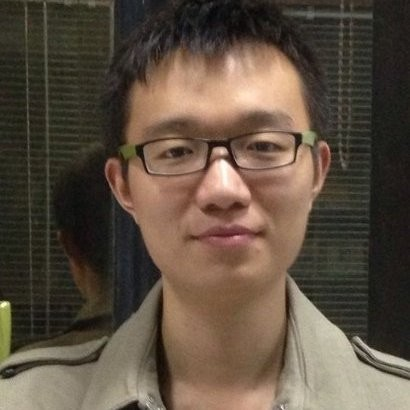
Di Huang
CEO, World Engine AI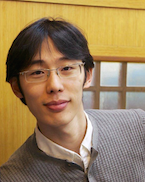
Joseph J. Lim
Associate Professor, KAISTSponsors
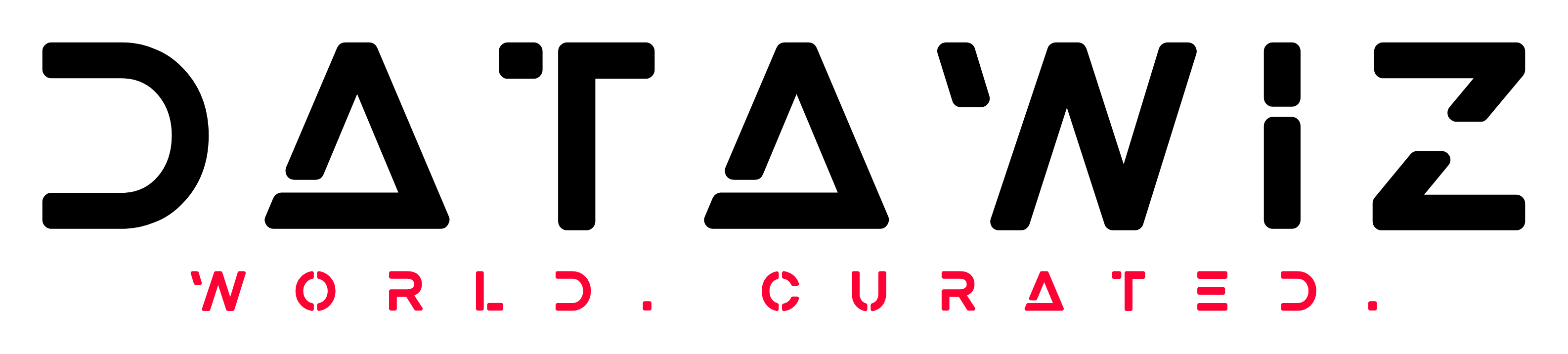
DataWiz
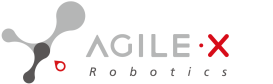
AgileX
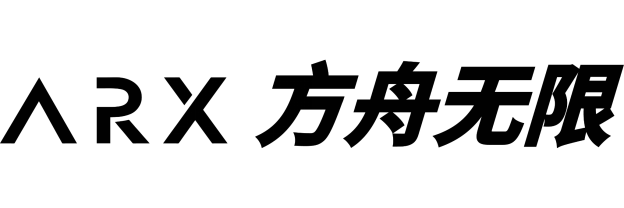
ARX
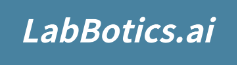
Labbotics
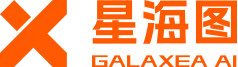
Galaxea
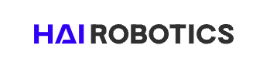
HAI robotics
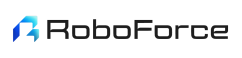
RoboForce
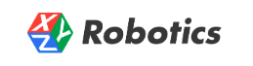
XYZ Robotics
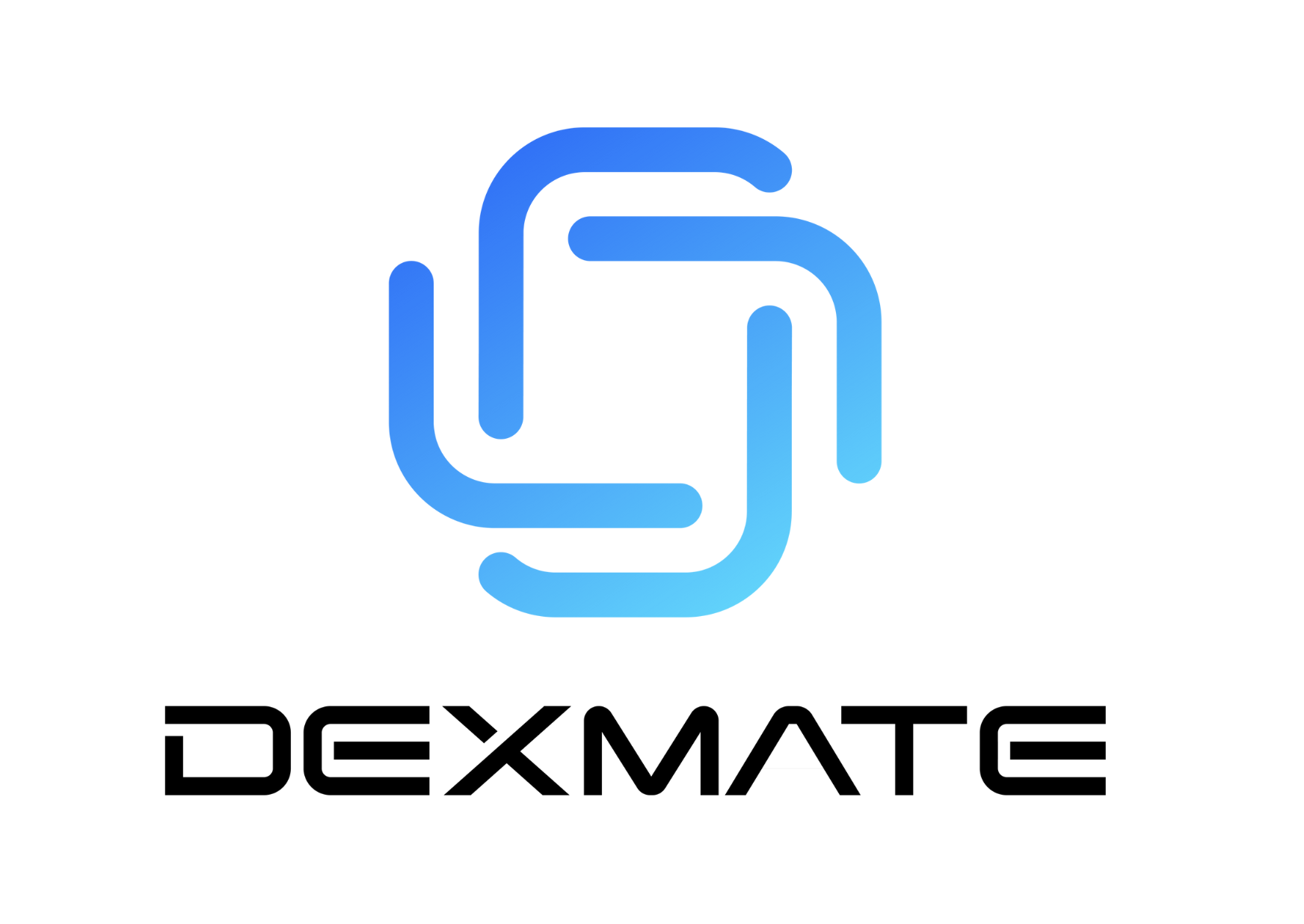